Can You Use Art Plaster to Make a Mold
Casts, copies, the real and the replica. Image: Annalice creighton / ANMM.
Casting and mould making are simultaneously the stuff of specialised creative and scientific endeavours and the backbone of mass production. From fountain heads and amulets to the haunting plaster figures that are now synonymous with this ill-fated metropolis, this calendar month'south craft spot is inspired by the use of casting and moulds in ancient times to create the artefacts that were featured in our previous exhibition Escape from Pompeii.
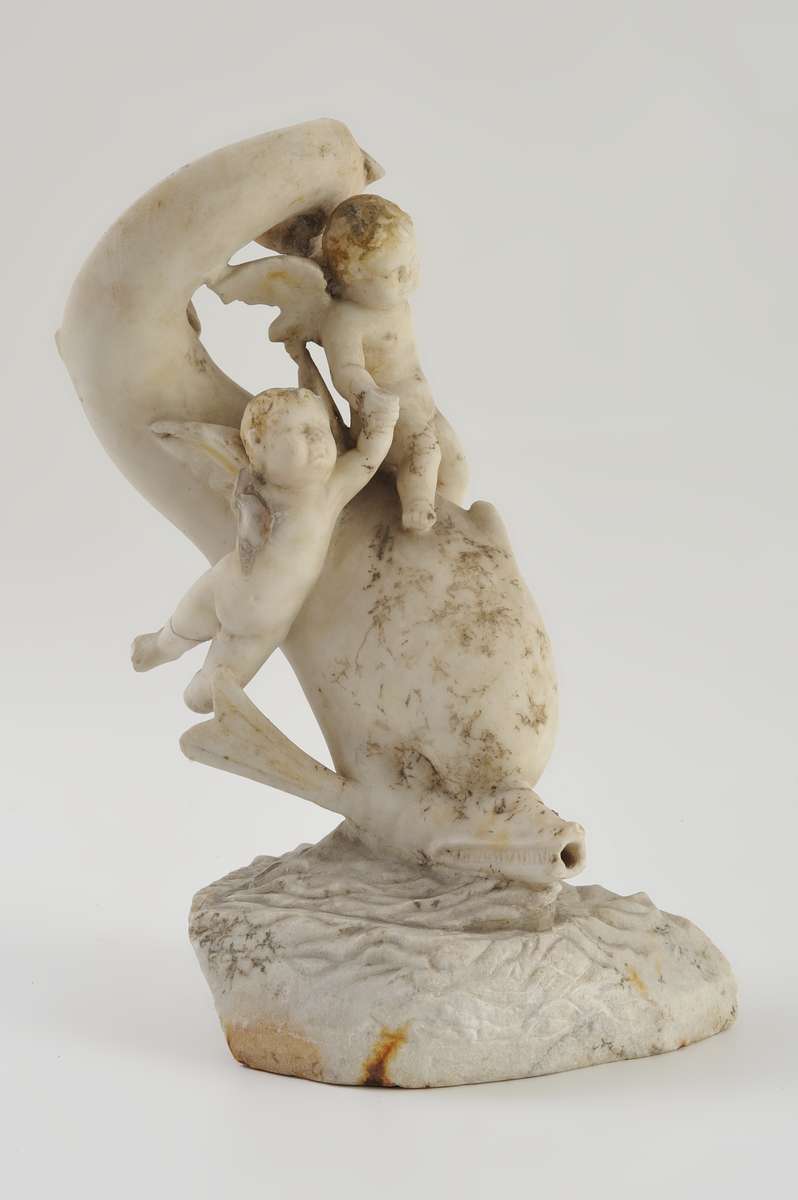
Fountain head with two putti riding a dolphin. Lent by the Soprintendenza Archeologica Di Pompeii.
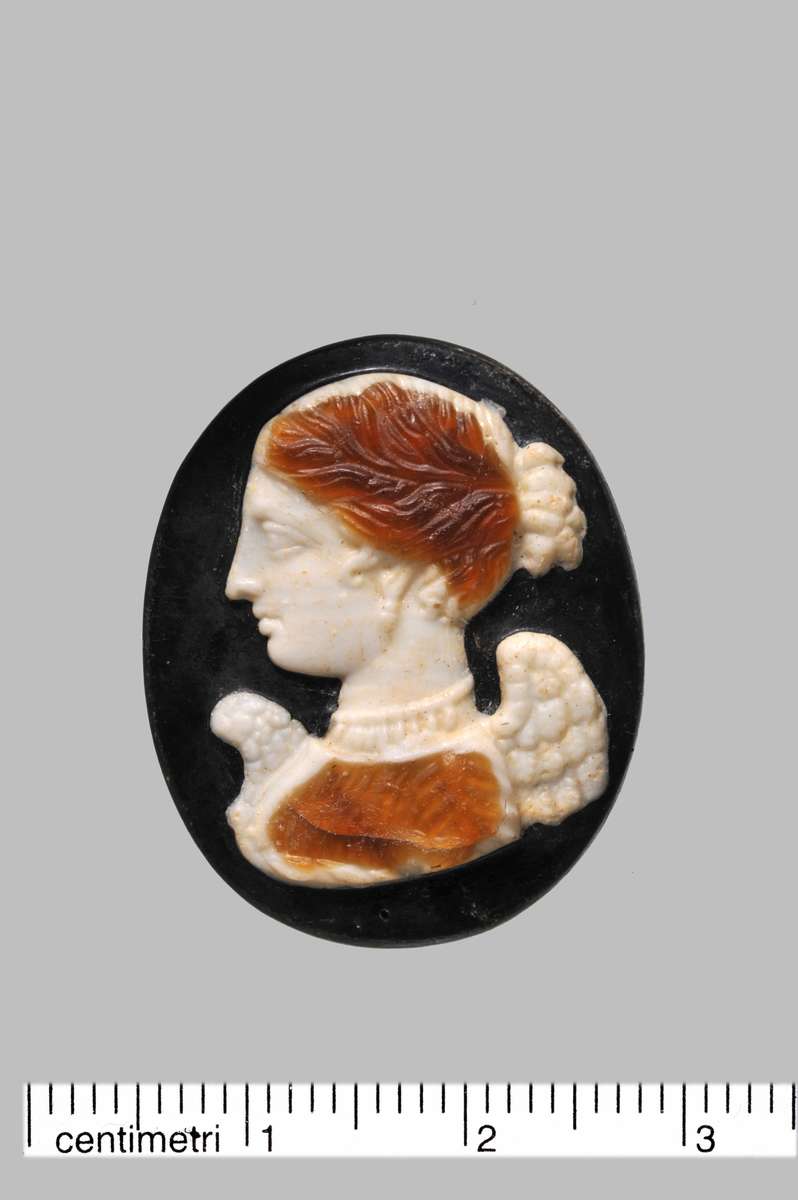
Glass paste cameo of Nike (Victory). Lent by the Museo Archeologico Nazionale di Napoli.
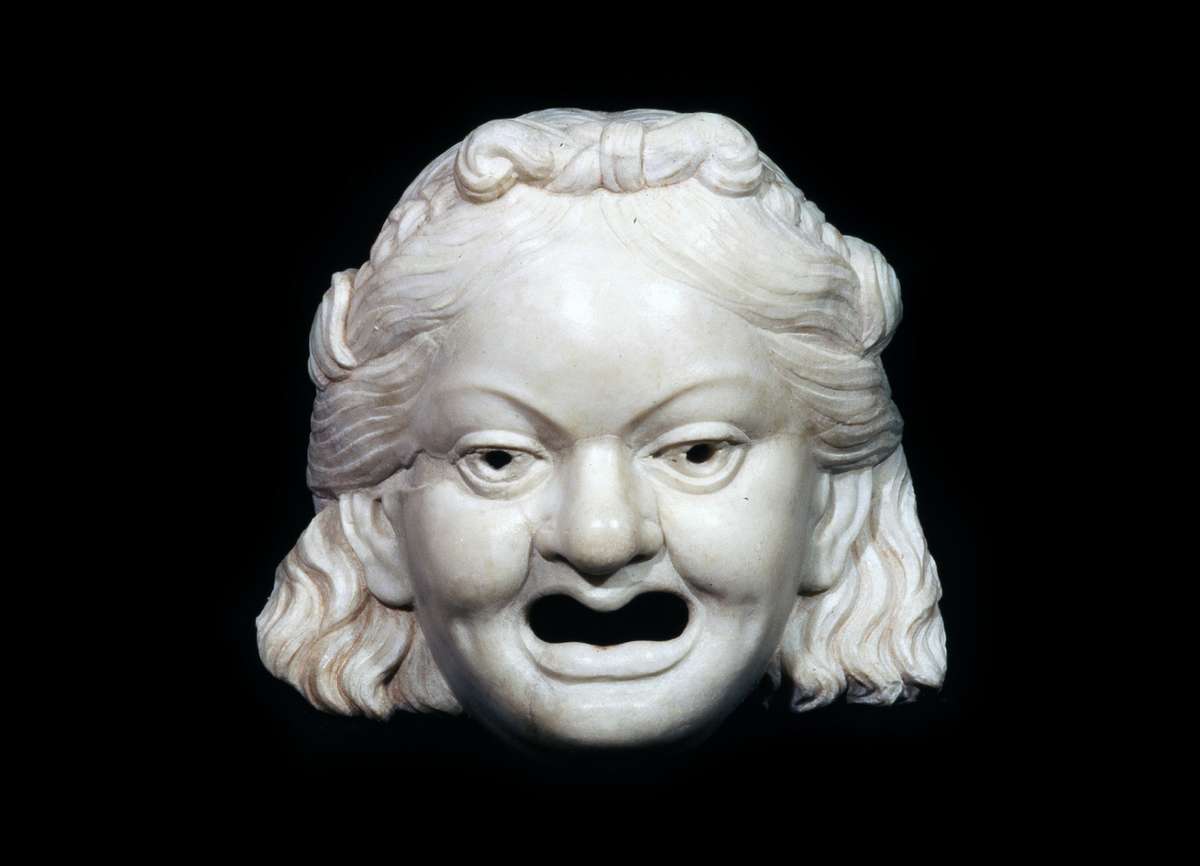
Fountain head with confront of an old woman. Lent by the Museo Archeologico Nazionale di Napoli.
The flows of fine ash that followed Vesuvius' eruption created a kind of mould – a detailed hollow impression – where any organic materials one time were. Casts have been produced from these ever since the clever Guiseppe Fiorelli, Manager of the Excavations in 1864, decided to endeavor pouring plaster into these mysterious hollows. This technique has enabled detailed body casts to exist made of these first-century Advertizing Romans in their final hour and has even been used to investigate the type of plants they grew in their gardens. Casting was also a common method of artistic product in the Roman Empire, from decorative rims to jewellery and mass production of statues.
Casting and mould making tin be incredibly complex and challenging, but it tin also be as easy as brushing on a piece of wet paper pulp or sticking your fingers into a cup filled with silicon. So here I've put together my favourite techniques for beginners, all piece of cake, pretty cheap and with a range of materials from the arts and crafts box, the hardware store or speciality suppliers and then yous can pick and choose what level of endeavor and experimentation y'all're up for. These are not the precise, technical methods that you would use for a beautiful lost-wax bronze sculpture but they are quick and like shooting fish in a barrel for beginners of almost any age.
Fix
You will need:
- A couple of plastic drop sheets and/or old sheets (whatever you would use for messy activities like painting)
- A bucket of water and sponge as well as a textile for whatsoever spills
- Cardboard boxes
- Painting apparel or apron
- Safe gloves
Silicone loving cup mould
Silicone cup mould. Epitome: Annalice Creighton / ANMM.
Silicone may be the about expensive material listed hither but it's likewise i of the easiest to work with: peel safe, quick curing and the moulds are very durable, flexible and able to cast lots of dissimilar materials.
But hither's the showtime dominion of casting: never similar with similar. Don't pour a silicon cast in a silicone mould or it will stick to itself.
If this kind of silicone is out of your price range there are some hardware store silicone hack recipes if you take fourth dimension to experiment, or latex is cheaper though not quite every bit like shooting fish in a barrel and reliable for beginners.
Materials
- Plastic cups
- Stirrer (tongue depressors work well)
- Pinkysil or other 2 part silicone mixture (this activity used almost $x of pinkysil)
- Kitchen scales
- A tiny bit of clay or plasticine
- Simple object to cast, such as a figurine, a light bulb. Something without holes or porous surfaces. Follow these guidelines for choosing your object.
- Casting textile of your selection: Wax, crayons, plaster, chocolate, expanding foam…
- Arts and crafts knife
- Masking tape
Gather your materials. Image: Annalice Creighton / ANMM.
Instructions
STEP 1. Plant your object at the base of the disposable cup, in a shallow bed of plasticine or dirt. You volition lose the detail on wherever the object is planted in the clay so cull the function that matters least.
Step one: Place your object in a dispensable cup to create a mould. Epitome: Annalice Creighton / ANMM.
STEP 2. Mix the silicone thoroughly as per the instructions on the pack. Pour it into a 2nd cup for extra mixing, as uncured bits can destroy your mould.
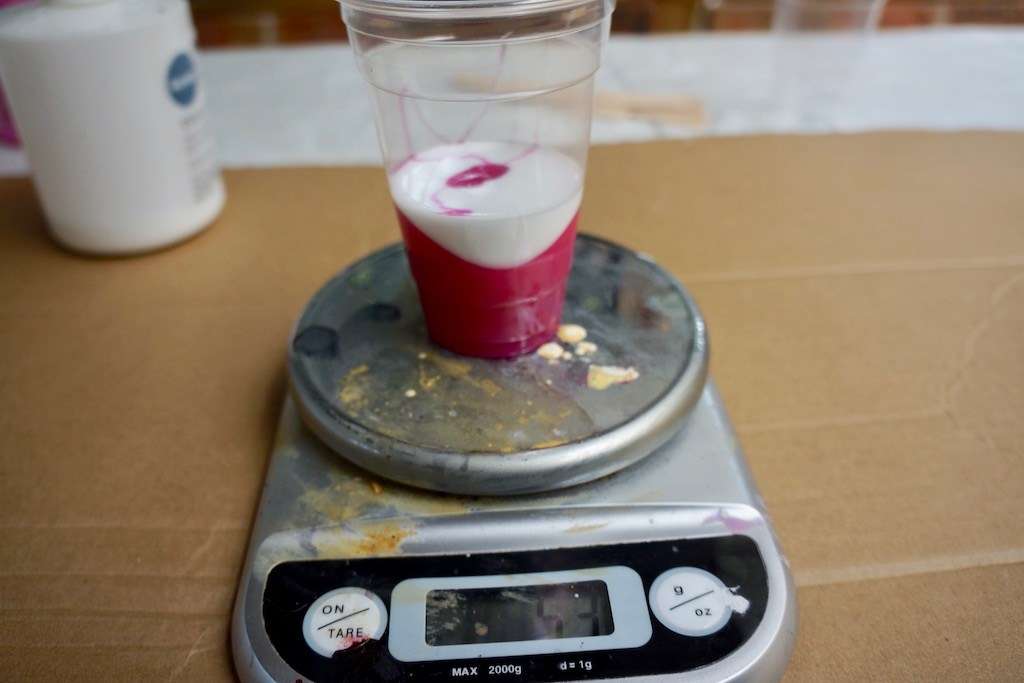
Image: Annalice Creighton / ANMM.
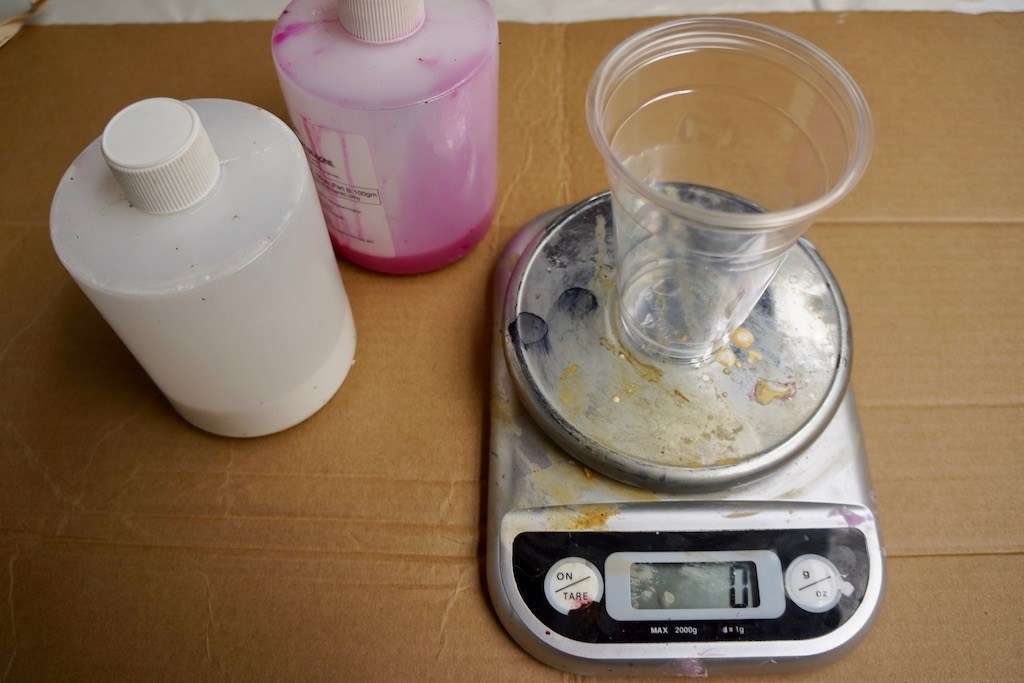
Prototype: Annalice Creighton / ANMM.
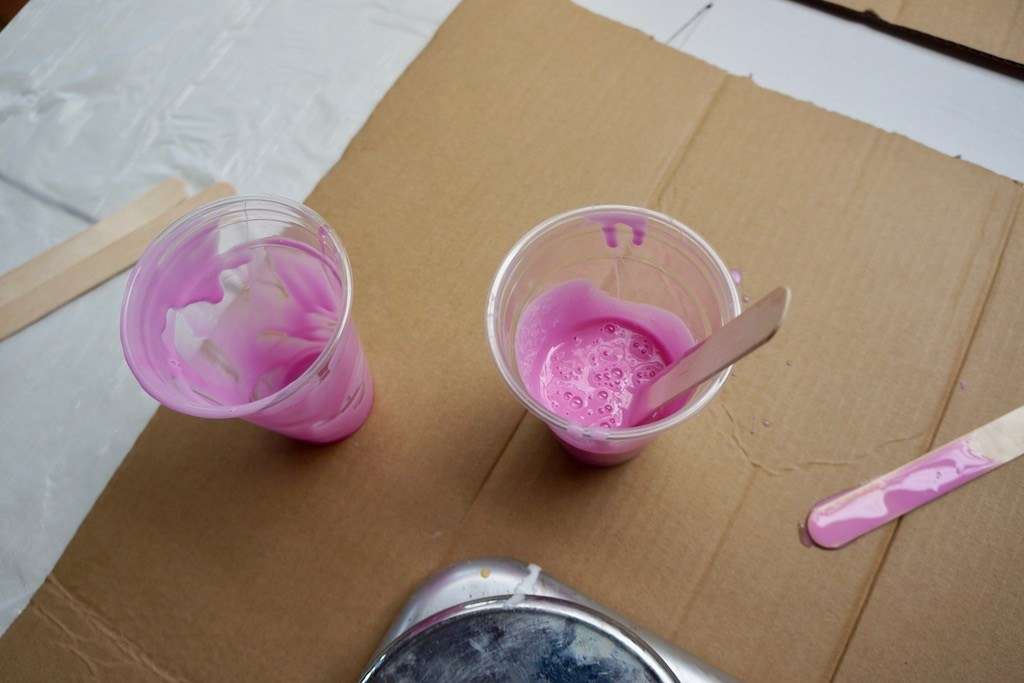
Image: Annalice Creighton / ANMM.
STEP three. Cascade the silicone into the cup with your object and let it dry for 15 mins.
STEP 3. Pour the silicone into the cup with your object and allow it dry. Epitome: Annalice Creighton / ANMM.
Step 4. Carefully use scissors to free the silicone mould from the plastic loving cup.
Because we haven't created a technically correct mould, with proper registration keys for the two parts, we're going to crook and slice a part through the mould in a zig-zag direction but to half or two-thirds its length. That we tin can easily remove the casts without breaking them.
HINT: This step will definitely need a responsible adult to complete.
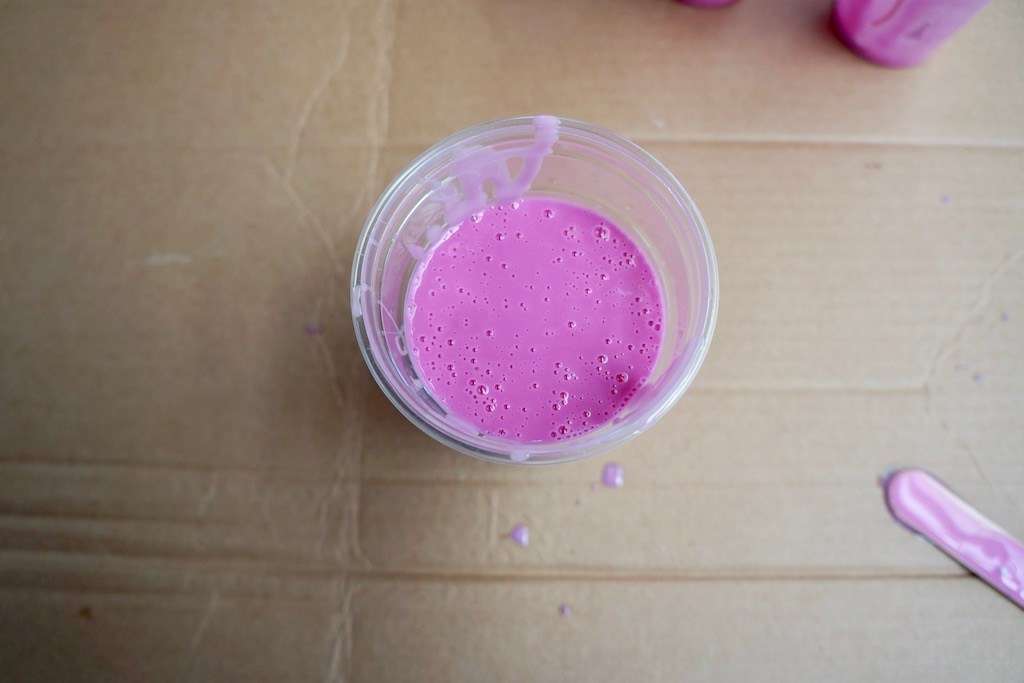
STEP 5. Pop your mould down on a level surface, masking tape it together and start pouring your first cast.
Stride five: Ready, set, cast! Image: Annalice Creighton / ANMM.
Glove mould with plaster bandage supports
Bodycasting. Image: Annalice Creighton / ANMM.
Got some silicon only desire to arrive last for a long time to go maximum value? This technique uses a thin coat of silicon, then makes a support out of plaster bandages. This is great for bodycasting small sections similar fingers or feet.
Materials
- Plastic cups
- Stirrers ( tongue depressors work actually well)
- Pinkysil (or other two-office silicon mixture)
- Kitchen scales
- A paint castor that you're happy to ruin in the process
- Plaster bandages (or some porous fabric to dip in some plaster)
- water
- Your easily/ feet or someone else's (even easier!)
Gather your materials. Image: Annalice Creighton / ANMM.
Instructions
STEP 1. Mix a small amount of silicon (nearly 60g) as per the instructions on the pack. Pour it into a 2nd cup for extra mixing to be safety, as uncured bits can destroy your mould. Yous can always go back and make a 2nd batch if you run out – unless you are casting your own hand in which instance doing anything that requires two hands while the silicone is wet is quite a challenge.
Stride 1: Mix the silicon, according to the instructions on the label. Image: Annalice Creighton / ANMM.
STEP two. Paint your silicon onto the surface of your non-dominant hand/fingers, like you lot are icing a block. Keep layering the silicon to build up an even, thorough coverage, not too frail or thin. Nails and fingertips will require extra as they are prone to bubbles and breakages. If at that place are thin patches once the first layer it is cured, reinforce these areas with a little extra silicon.
Step 2: Paint the silicon on. Epitome: Annalice Creighton / ANMM.
Pace 3. Once silicon is dry you can outset applying plaster bandages to class a back up glove all around the silicone mould. Ideally, you want the mould to be able to stand up so you can pour molten liquids into information technology. You can also employ boxes/cups/newspaper to assist with your back up structure if needed.
Step three. Remove the dried silicon. Image: Annalice Creighton / ANMM.
STEP 4. Plaster takes a while to dry so one time it's starting to harden y'all can wriggle out of the mould at some point and leave it on a supported surface as it dries.
Step 4. Apply plaster bandages to back up the mould. Image: Annalice Creighton / ANMM.
One time this is dry yous're all gear up to offset pouring casts.
2-part plaster mould
This activity is one of the cheapest techniques but besides the near time-consuming. If you don't choose the right object, use enough lubricant or fill up in the undercuts in your object well you lot could easily end up with a bang-up lump of plaster stuck to an object.
A shell csat using the 2-part plaster mould techinue. Image: Annalice Creighton / ANMM.
Materials
- Vaseline or cooking oil spray
- Plaster of Paris (well-nigh $viii/three kg from hardware stores)
- Clay or plasticine
- Modest cardboard box
- An uncomplicated pocket-size object such as a seashell. Plaster isn't flexible so cull something that is easily going to popular out of that mould when information technology sets.
Gather your materials. Image: Annalice Creighton / ANMM.
Instructions
Footstep 1. Identify the object in the cardboard box. Brand sure the box is non also big, merely big enough for your object.
Bury your object upwards to halfway in plasticine or cheap clay and rub that lump of clay into the bottom of the box. Ensure there'southward no cracks or united nations-dirt-filled crevasses where the plaster can run wild and terminate upward trapping your object inside your mould.
Step i. Place your object to re-create in the box. Image: Annalice Creighton / ANMM.
Yous can apply tape along the edges of the box to ensure its sealed tight.
STEP two. Pop some 'keys', little indentations, in the plasticine effectually the surface of your object with the cease of a paintbrush so that you lot can create a ii-part interlocking mould. Vaseline up your dirt and your object VERY THOROUGHLY. Plaster will stick to any unlubricated surface (except the plasticine of course).
Step 3. Create 'keys' in your mould by indenting the plasticine with the end of your paint brush. Image: Annalice Creighton / ANMM.
STEP 3. Pour the mixed plaster into the box. Sit it aside to dry.
Pace 3. Pour the mixed plaster into the box. Sit it bated to dry. Image: Annalice Creighton / ANMM.
STEP 4. Tip the box over or tear abroad to remove your plaster mould.
Pace 4. Tip the box over or tear away to remove your plaster mould.
Pace 5. Allow the plaster to dry thoroughly. Place the plaster mould on the bottom of the box (if y'all've destroyed your box rebuild another ane to fit) and supervene upon the object.
Step five. Place the plaster mould on the bottom of the box and replace the object. Image: Annalice Creighton / ANMM.
Footstep half dozen. Add a clay "pour spout" to this side of the object and lots more Vaseline to coat the mould and the object (if this isn't washed properly y'all volition end up with a dandy lump of plaster instead of a mould!). If the underside of the object has holes and complicated undercuts, fill it in with clay then that y'all have a simple/ polish surface for the mould.
Step 6. Coat the object and sprout with lubricant. Prototype: Annalice Creighton / ANMM.
Pace 7. Pour more plaster on summit and permit to dry out thoroughly (might take a day or so).
Pace 7. Pour more plaster on top and allow to dry out thoroughly. Prototype: Annalice Creighton / ANMM.
STEP 8. Cut off the box and gently pry apart your mould to remove the object. Y'all might need to fleck away at the edge with a tool to get it open at start.
STEP 9. Grease up the mould over again. Pop the two sides together and you're prepare to start casting.
Cheats method paper casting
Paper casting. Image: Annalice Creighton / ANMM.
Materials
- United nations-dyed tissues or hand-made paper lurid
- A chubby brush
- A uncomplicated object – eg. a plastic mannequin, a decorative frame, a plaque, a silicone mould
- Water in a tray
Gather your materials. Image: Annalice Creighton / ANMM.
Instructions
Step 1. Make your paper pulp by soaking the tissue in a tray of water. Gently lay the newspaper strip by strip onto the object.
Stride 1. Make your newspaper pulp by soaking the tissue in a tray of water. Epitome: Annalice Creighton / ANMM.
Pace two. Pat downwardly gently to capture the object detail with a brush.
Step 2. Pat down gently to capture the object detail with a castor. Paradigm: Annalice Creighton / ANMM.
Footstep iii. Keep layering the newspaper until you lot've congenital up a squeamish newspaper " skin" on the object. Allow to dry and gently remove from the object.
Newspaper casts are a cast without a reusable mould per se then your work is done, brush a loose paint over information technology, pigment it (just non with anything besides wet!), decorate it or hang it up!
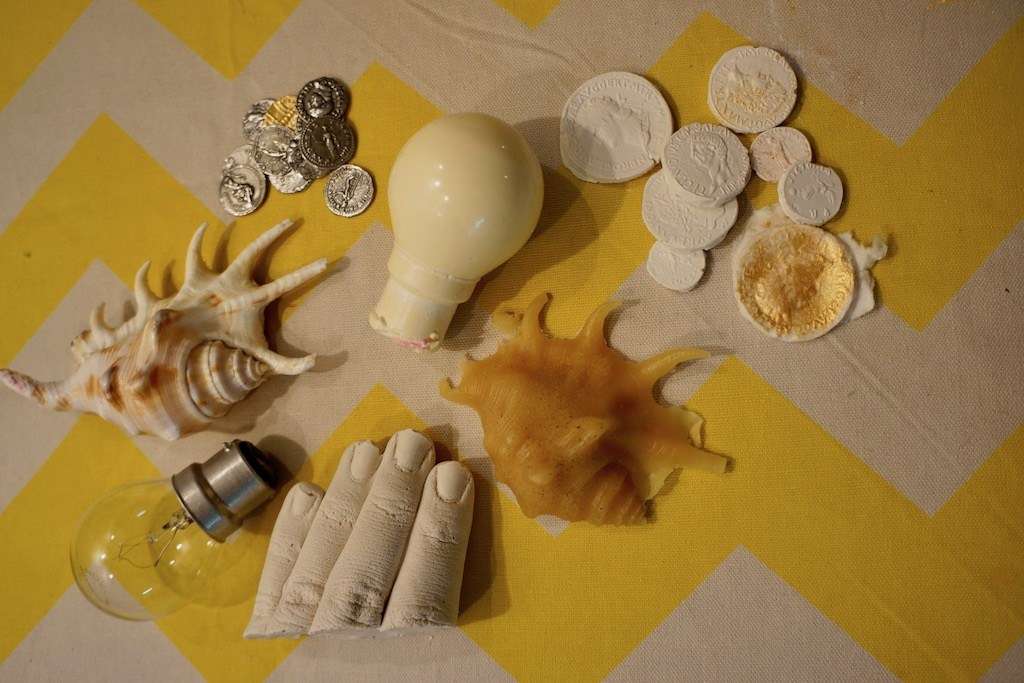
Finished casts and objects. Epitome: Annalice Creighton / ANMM.
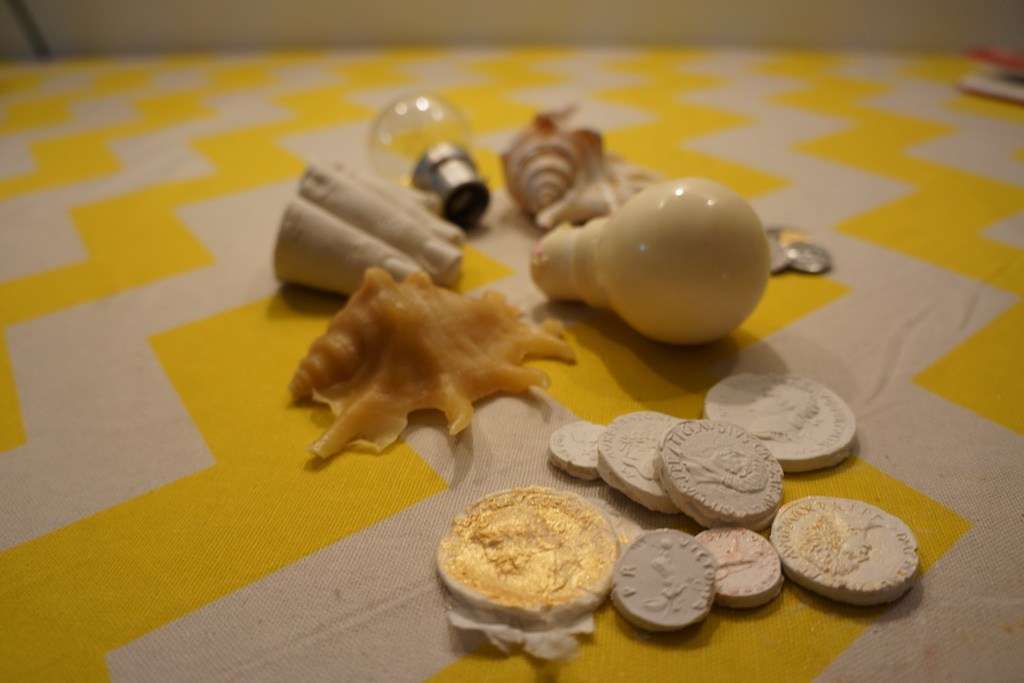
Finished casts and objects. Paradigm: Annalice Creighton / ANMM.
As for casting materials to pour into your silicon moulds- your imagination is the limit! I've had groovy fun with expanding foam, plaster, wax, chocolate, double force jelly, melted crayons and soap, pretty much annihilation that can get apace from melted to solid is a possibility! Experiment till your heart's content.
Source: http://www.sea.museum/2017/03/29/casting-the-past-how-to-make-cheap-easy-moulds-and-casts
0 Response to "Can You Use Art Plaster to Make a Mold"
Post a Comment